1. 热塑性弹性体介绍
热塑性弹性体TPE/TPR,又称人造橡胶或合成橡胶。热塑性弹性体在常温下具有橡胶的弹性,高温下具有可塑化成型的一类弹性体。
其产品既具备传统交联硫化橡胶的高弹性、耐老化、耐油性各项优异性能,同时又具备普通塑料加工方便、加工方式广的特点。可采用注塑、挤出、吹塑等加工方式生产,水口边角粉碎后100%直接二次使用。既简化加工过程,又降低加工成本。因此热塑性弹性体TPE/TPR材料已成为取代传统橡胶的最新材料,其环保、无毒、手感舒适、外观精美,使产品更具创意。
2. 配方及原材料特点
(1) 配方:SBS/SEBS+PP+OIL+添充剂
(2) 原材料特点:SBS/SEBS,原材料堆密度很低,为0.2kg/m3,很轻,发泡状,占据空间大,不易加入到螺杆中。OIL:加入到挤出机中成为润滑剂,物料输送减慢。
3. 生产工艺
配料——预混合——熔融混合——切粒
4. 双螺杆挤出机选型
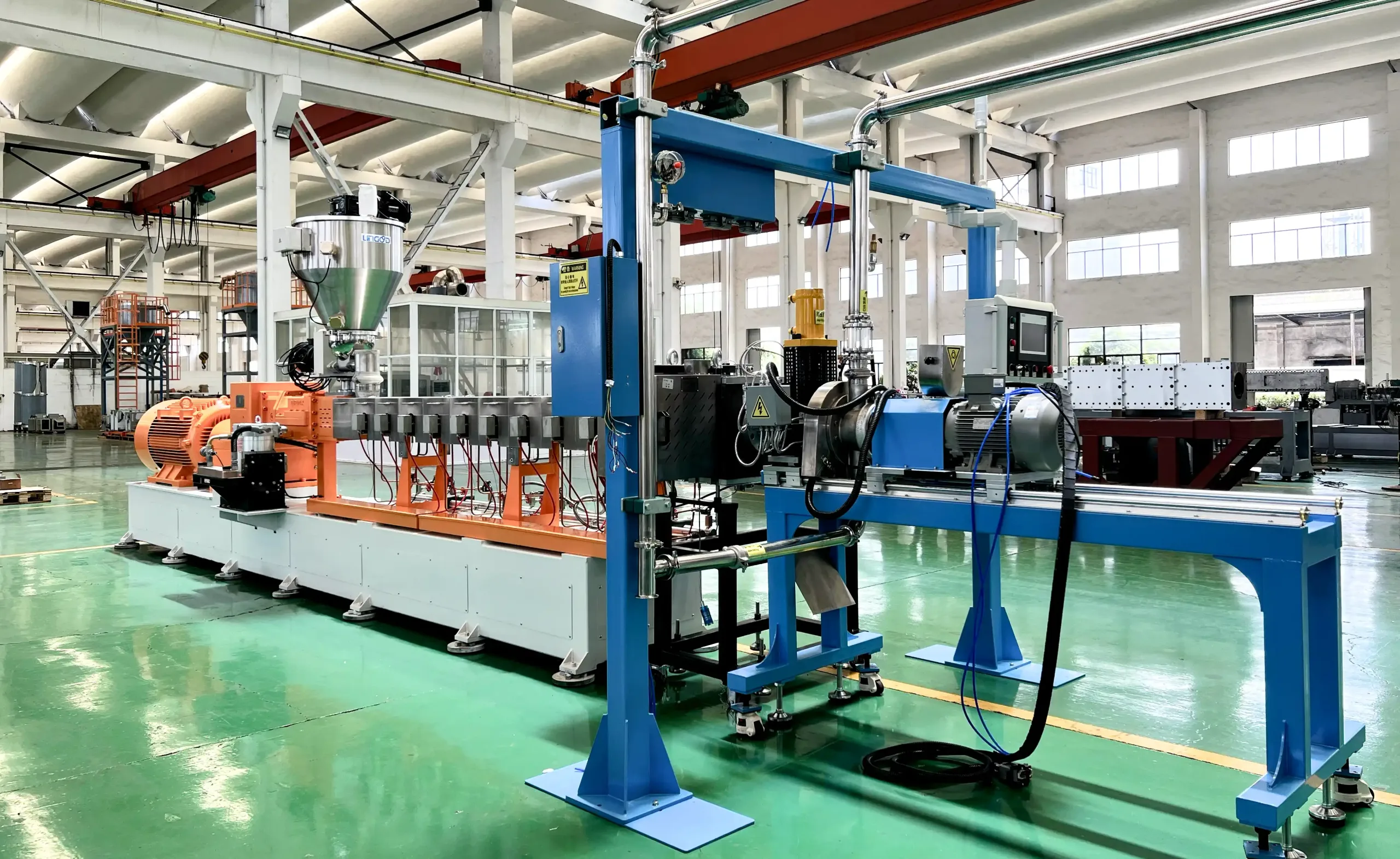
在众多混炼塑化挤出机中,平行同向双螺杆挤出机以其优异的混炼塑化性能、良好的螺杆自清理功能、螺杆筒体的“积木式组合”功能,在塑料配料混炼中得到非常广泛的应用,在热塑性弹性体生产中也得到充分的应用。
在热塑性弹性体的生产设备选择中,双螺杆挤出机的配置和选型是非常重要的一个环节,对以后的生产具有重要影响。选型主要有如下特点:
4.1选用平行双螺杆挤出机
4.2螺杆直径:根据生产规模,一般选用螺杆规格在50mm到90mm机。
4.3长径比L/D:≥44,一般为48
4.4螺杆转速:≥600rpm
4.5螺杆材质:建议选用耐磨型兼耐蚀型,如采用W6Mo5Cr4V2高速钢,筒体宜选用高耐磨型待衬套结构,如内衬a-101高耐磨合金。
4.6 电机功率:大功率。
4.7 齿轮箱:速比小,高扭矩等级,比扭矩通常M∕A3≥8。
4.8主机配置:要有足够的长径比,使物料充分受热和剪切塑化;入口要有大的自由容积,增强吃料效果,要有良好的排气功能,脱除低分子物和单体。
5. 加料方式
由于原料是粉状、粒状混合物,考虑物料特点及输送效率,建议采用双螺杆喂料机,并带搅拌。不建议强制填塞喂料。
6. 螺杆组合及筒体设计
6.1 加料段:由于SEBS/SBS料为膨松状,加入到螺杆上不易吃料,故采用大导程、深螺槽螺纹元件。机筒加料口采用长方形。
6.2 输送段:选择大压缩比,使物料迅速压缩、输送。
6.3 混炼塑化段:选用较多的捏合块,可选用30度、45度、60度捏合块,与密炼转子配合使用,捏合块实现分布混合。密炼转子使增加拖拽拉伸,不要增加了物料的分散性。
6.4 排气段:要有较大的排气空间,通常采用大导程螺杆元件;在排气口前螺杆上设置反向元件,实现建压功能。
6.5 均化计量段:要有强的输送功能和稳流功能,以实现挤出压力的平稳和造粒的均匀性,通常采用小导程元件和大于6的长径比。
7. 真空排气
用平行双螺杆挤出机生产TPE时,使用抽真空,可去除产品中的低分子挥发物、异味,对提高产品质量是很有好处的。
真空口很容易冒料,如何控制真空口不冒料是关键。
针对配方及操作工艺,一般情况下真空口冒料的原因素有:
①.油加入太多。物料流动速度加快,在排气孔附近物料输送失衡。
②.加工温度偏低。
解决的办法是改进配方,提高工艺温度;
针对挤出机:真空口要设置在合适的位置,选用合适的挡料块,设计合理的螺杆结构。
通过上述方法仍无法解决真空口冒料,就必须重新组合螺杆。
8. 切粒方式
TPE一般选用水环切粒、水下切粒、风冷模面切粒,根据物料性能要求选择。如硬度在10A以下的物料选用风冷模面热切方式。
这三种切粒方式的特点比较:
水环切粒 | 水下切粒 | 风冷模面切粒 | |
---|---|---|---|
切粒特点 | 干面切粒 | 水中切粒 | 干面切粒 |
冷却特点 | 水冷 | 水冷 | 风冷 |
生产能力 | 适中 | 较大 | 较小 |
9. 提高挤出机产量的方法
(1) 提高螺杆转速,就必须使用大的L/D,确保物料充分塑化。
(2) 采用侧喂料,可使产量提高40%。在许多厂家得到应用。
案例
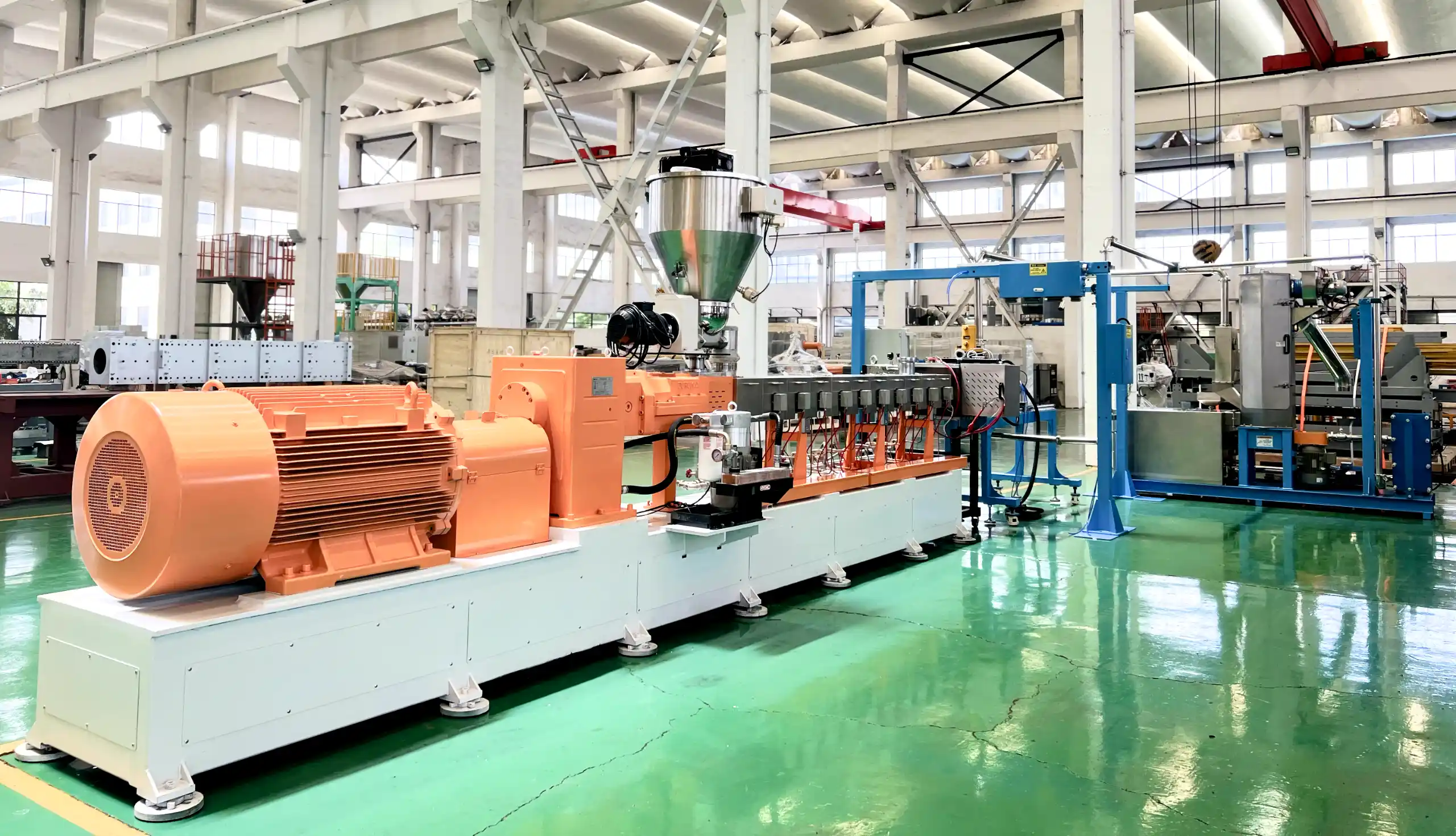
TPE造粒
产品性能:邵氏硬度55A,密度0.98
SHJ-75H高性能同向双螺杆挤出机
螺杆直径:72mm
螺杆长径比:L/D=48,
螺杆转速: 600r∕min,
挤出机功率:250 KW
操作温度:190℃、200℃、210℃、210℃、210℃、210℃、200℃、200℃、190℃、180℃、170℃